Loading Dock Slots
Definition of Loading dock
Begin planning inbound or outbound loads within those constraints and communicate it to carriers. Slot incoming/outgoing shipments into the 60 minute time slots on the dock schedule. Communicate those pickup/delivery times with carriers. Enforce the rules and PDCA. Typically early routes will need to wait before they can approach the dock, and late routes will need to be rescheduled with no demurrage penalty incurred at the dock. Begin planning inbound or outbound loads within those constraints and communicate it to carriers. Slot incoming/outgoing shipments into the 60 minute time slots on the dock. Inefficiencies at the dock can cause long lines of trucks outside shipping facilities, delayed deliveries and increased driver wait times—plus the added cost of steep detention fees. Transporeon Dock Scheduling shows your loading and unloading capacity in a digital schedule, and gives both you and your carriers visibility into the time slots.
1.Noun. A platform where trucks or trains can be loaded or unloaded.
Generic synonyms:Platform
Lexicographical Neighbors of Loading Dock
loaded loaded down loaded down(p) loaded for bear loaded word loaden loadened loadening loadens loader | loaders loadeth loading loading(a) loading area loading dock (current term) loading dose loading screen loading screens loading space | loading spaces loading zone loading zones loadings loadmaster loadmasters loads loadsa loadsamoney loadspace |
Literary usage of Loading dock
Below you will find example usage of this term as found in modern and/or classical literature:
1.The Iron Ores of Lake Superior: Containing Some Facts of Interest Relating by Crowell & Murray (1920)
'At the mine office is kept a carefully made box containing slots representing the pockets of the loading dock, each slot bearing a number corresponding to ...'
2.Lumber, Its Manufacture and Distribution by Ralph Clement Bryant (1922)
'... kilns to rough-dry sheds, to the planing mill, or to the loading dock; and air-dried lumber from the yards to the planing mill, or to the loading dock. ...'
3.Proceedings by American Society of Civil Engineers (1903)
'Much of it, however, was used by the contractors for filling the cribs of their loading dock, ballasting track and other purposes. ...'
4.Communities at Work: Addressing the Urban Challenge by Diane Publishing Staff (1998)
'Approach Recent visitors to The loading dock warehouse in Baltimore, Maryland, found lumber, windows, solar panels, a maple gymnasium floor, toilets, tubs, ...'
5.How to Reduce Energy Costs in Your Building by DIANE Publishing Company (1983)
'As with loading dock comfort, the more comfortable you can keep the auto service area the more productive the people working there are likely to be. ...'
Other Resources:
Search
To design efficient loading docks, determine the:
- Types and numbers of trucks that will use the docks
- Dimensions of the loading docks and doors
- Characteristics of the facility processes
Then, consider the dock height, loading bay width, and dimensions and layout of the building interior.
Truck Specifications
Determine the types and dimensions of the trucks that will use the docks. List each truck’s length, width, height and bed height.
See Figure 21 through Figure 26 for the dimensions of common truck and trailer designs. Note that weight of freight can cause a variance of up to 6 in. in trailer and bed heights. The dimensions may also be affected by air suspension systems. Use Figure 21 through Figure 26 for preliminary design, but obtain actual truck dimensions before making final design decisions.
Figure 22: Semitrailer
Figure 24: Refrigerated Truck
Figure 26: Flatbed Truck
Sea Containers
Sea containers and refrigerated containers can have trailers with heights of up to 62 in. Facilities that must service sea containers may also frequently service low-bed trucks. The height difference can be from 30 to 62 in. Consider designing docks of various heights or installing equipment such as hydraulic truck levelers or elevating docks. Typical container sizes are listed in Table 5.
Table 5
Underride Protection Bars
The underride protection bar, called the Rear Impact Guard (RIG) bar, is mounted at the rear of the trailer (Figure 27). Restraint devices attach to the RIG bar to prevent the truck from being driven away before loading or unloading is complete.
Set the Dock Height
The most important characteristic of the loading dock design is the height of the dock. The dock height must match the height of the docking trucks. The height difference between the dock and the trailer bed should be as small as possible. The dock leveler bridges some height difference, but the incline should not be too steep. A steep incline can cause insufficient forklift underclearance, and it increases maintenance demands on the equipment.
To determine the dock height, find the midpoint of the bed heights of the expected trucks. Most trucks require a dock height of between 46 and 52 in.
See Table 6 for dock heights that create level docks for common types of trucks.
Table 6
NOTE: Truck beds will rise and lower during loading and unloading.
If the driveway is recessed, the dock height should be lower (Figure 28). A recessed parking area may lower the truck bed height by 6 to 10 in.
This is particularly important when a driveway approach declines to a level surface in front of the dock, and when the truck or trailer has its wheels positioned well forward of the rear of the vehicle.
For example, in Figure 29, the drive approach is an 8% decline leading to a level concrete pad at the dock. A typical trailer bed, which is at a 48 in. height (HL) from the decline drive, will be at approximately 40 in. (HD) at the dock. Therefore, if the dock is intended to service trailers with 48 in. bed height, the dock height should be at 40 in.
HL = Bed height when level
HD = Bed height at dock
Figure 29
Design the dock height based on the specific parameters of driveway slope, geometry of the recessed parking area, and bed heights of the expected trucks unique to your building.
If the expected trucks have very high or low bed heights, provide dedicated dock positions with special driveways and equipment, such as an elevating dock (Figure 30).
For open docks, where the trailer doors are commonly opened after the trailer is parked, design a dock height low enough for the door clamp hooks to clear the dock as they are opened (Figure 31). 51 in. is a common dock height for this situation. If the driveway is recessed, lower the dock height further since the doors swing down slightly as they are opened. Lower the dock by about 1 in. for each 1% of recessed driveway grade.
Figure 31
Set the Loading Bay Widths
Each truck bay should be at least 12 ft wide to provide enough space for the trailers, which are 8’0″ to 8’6″ wide, to back squarely to the dock. To reduce congestion, design 14 ft wide bays. If swinging trailer doors will be opening or closing at the dock, the center distance should be at least 14 ft (Figure 32).
Select Dock Doors
A dock door is required for inside/outside loading docks. The most commonly installed doors are manually operated and are either an overhead sectional door or a roller door. A sectional door is smoother and quieter than a roller door because of rollers that run inside of tracks. Other advantages of a sectional door are:
- They are thicker and stronger than a roller door
- They can be insulated
NOTE: Install door track protectors to protect the door tracks.
Common dock door dimensions are 8’0″ in width with 8 ft, 9 ft or 10 ft heights. Consider extending the door 13 ft to 14 ft above the driveway and a minimum of 8’6″ wide if full access to the truck’s interior is required. Dock doors dimensions are determined by:
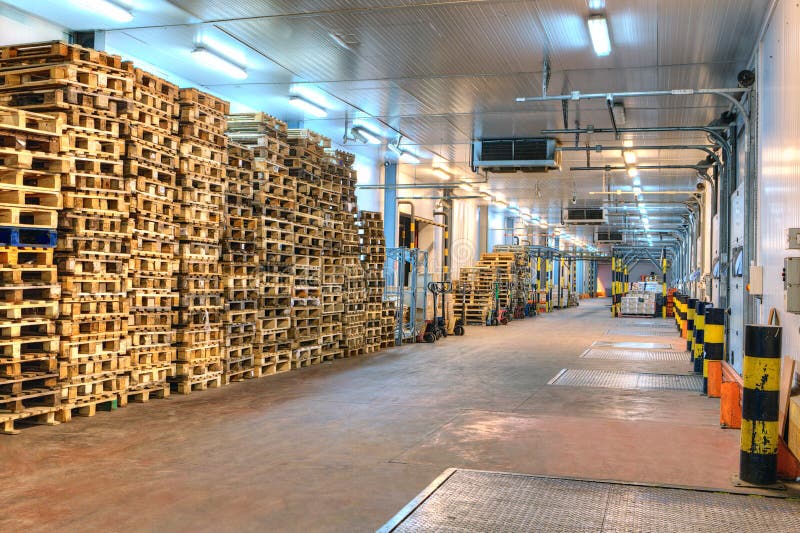
- Type of trucks being serviced
- Sealing system
- Environmental concerns
Determine Door Sizes

NOTE: The maximum trailer size limits are 8’6″ wide x 13’6″ high (varies by state). With a special permit, a flatbed may exceed the maximum width.
Widths
Determine the door sizes along with selecting the sealing system. Keep doors as small as possible – usually narrower than 8 ft – in temperature-controlled docks, where energy is lost through doors. Space the doors 12 ft apart to accommodate most trucks, sealing systems, and communication light systems.
Dock doors narrower than 8’0″ are commonly installed with compressed foam dock seals for temperature control of refrigerated operations.
9 ft wide doors should be used to service 8’6″ wide trailers. Side-by-side palletizing is simplified, potential for product damage is reduced, and oversized loads can be serviced.
The doors should be between 8’6″ and 8’0″ wide to allow for trucks to park off-center. A 10 ft wide door can be designed for oversized loads. Note that wider doors require more building space, which may not be available.
NOTE: Compression of seals may reduce the effective width and full access to trailer.
Figure 33
Heights:
Doors are typically 8 ft, 9 ft, or 10 ft high. 8 ft high doors can accommodate many loading and unloading operations where height is not critical, but cannot accommodate floor-to-ceiling loading (Figure 35). 8 ft high doors do not maximize the usage of the available height in the trailer, which leads to higher freight costs.
Figure 35
A 9 ft high door allows for improved floor-to-ceiling loading (Figure 36) as a higher load can pass through the door. Fuller, tighter loading makes for better space utilization with a decreased risk of product damage due to door impact. The 9 ft height suits a wide range of applications. However, in trailers with lower height there may be a gap between the trailer and the top of the door. The gap can be closed off with a dock seal or shelter.
A 10 ft high door services the full range of loading and unloading operations (Figure 37). 10 ft high doors accommodate trailers of heights up to and including high cube trailers and high cube sea containers.
Figure 37
To provide full access to the entire width and height of a full-size trailer, the dock door should extend the full height of the trailer (13 to 14 ft) above the parking area.
Design the Dock Interior
Loading Dock Slots Games
Design a forklift traffic aisle, 15 ft wide minimum, behind the loading ramps. This aisle provides better visibility, allows forklifts to maneuver behind the trailers, and permits two-way traffic parallel to the dock face. Aisles that are 15 ft or wider allow forklift drivers to drive straight onto the docklevelers, which reduces injury hazards and equipment stress (Figure 38).
Loading Dock Baltimore
Put restrictions into place that deter forklift drivers from driving parallel to the dock face (Figure 39), which can result in collisions with forklifts backing out of trailers.
Loading Dock Raleigh
Figure 39